COLD FORGING
KOMATSUの冷間鍛造
小松工業が冷間鍛造技術を追究する理由、それは切削加工より格段に多くのメリットがあるからです。
工程改革とコストダウンの決め手となる冷間鍛造技術のメリット
メリット
1
材料費が削減できる
第一は材料費が削減できることです。材料を削る切削加工と比べ、圧縮成形する冷間鍛造では材料のロスが一切ありません。材料コストが削減できる上に、資源(鉄)の有効利用にもつながります。
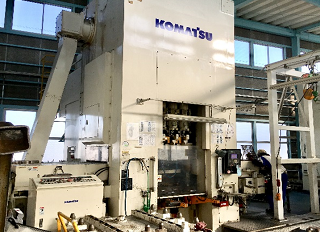
メリット
2
格段に速い加工スピード
第二に加工スピードがあります。切削の加工スピードが分単位であるのに対し、鍛造のスピードは秒単位。スピードが上がれば生産効率が上がりコストダウンにつながることは言うまでもありません。
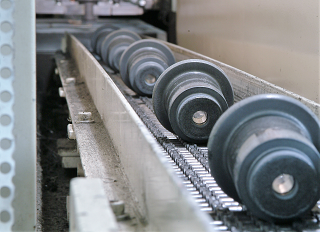
メリット
3
複雑形状に対応
第三は複雑な形状に対応できること。切削では不可能な形状も、鍛造なら実現可能です。仕上がりが高品質で、切削加工などの後工程が不要となれば、さらにコストダウンと効率化が図れます。
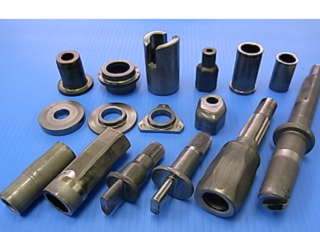
上記に加え、成型時の加工硬化を利用した熱処理廃止など多くのメリットがある反面、
冷間鍛造には一筋縄ではいかない局面もまたあります。
小松工業は独自の成形手法や周辺技術との連携を通して、冷間鍛造を使いこなすノウハウを蓄積してきました。
そのノウハウがお客さまからの高度なご要望に対応する秘訣ともなっています。
冷間鍛造が可能にした次代の技術、今まで培ってきた技術の集大成
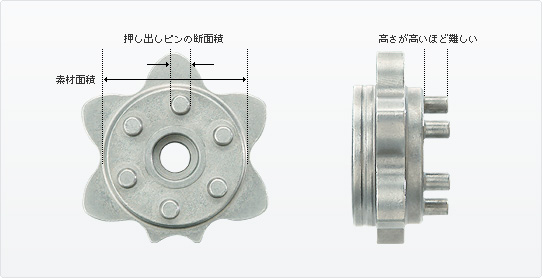
素材から凸状のピンを押し出す場合、素材の断面積に比べてピンの断面積が小さくなるほど(断面減少率が大きくなるほど)、また高さが高くなるほど難しい技術を要求されます。このふたつの困難をクリアしたのも、小松工業のより高い技術に挑むチャレンジ精神があったからです。
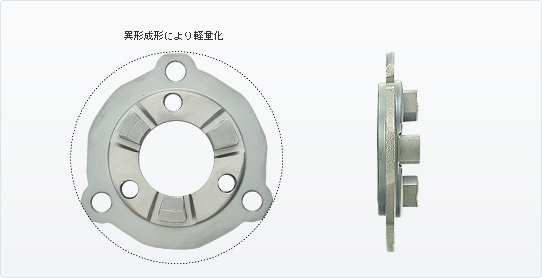
通常、熱間鍛造もしくは熱間+冷間の複合鍛造で成型するとされていた形状も、小松工業の常識では冷間鍛造オンリーで成型。加工スピードにもこだわり弊社独自の技術で、6箇所の穴を同時に打ち抜きます。また外周を異形に成形することにより製品の軽量化にも成功しています。