Pioneer of Komatsu

The challenge is to make impossible things possible
Chapter 2 - Problem about Material Shape
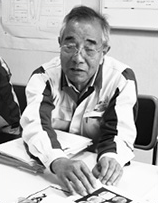
The problem was the shape of material in the previous process. At first, I tried with a round bar but the result was no good. Next, I tried using the plate material, but still no good at all. The material which shaved from round bar is becomes NG, and even i tried to make and strike the material of round irregular is shaped and strikes, it will be broken or cracked and become useless thing. The first and biggest challenge of this development was the material shape on previous process.
Nakamura, a cold forging master, has mobilized nearly half a century of his knowledge to search for the best material shape. More than 100 pieces of material are floating on his head. He makes dozens of them in reality and try to shot 5 to 6 pieces with cold forging. The dimensions of product were measured and flow line of the metal flow was examined. Once a week, it also involves production, and a half-day trial. This was silently done with Takeyama of production engineering.
It takes about half a year to reach a satisfactory material shape. Initially, implementation for the next model was planned, and team member focused their efforts on improving the degree of completion. By reporting the progress to the client companies one by one, the customer's expectations were also rising.