Pioneer of Komatsu

The challenge is to make impossible things possible
Chapter 1 - It was not like this.
"Oops!"
Everyone who involved in development project of the adjuster chain look each other to the first part created by cold forging technology. Member are cold forging master Nakamura Advisor, Naito with more than 35 years of production engineering experience,
Takeyama, the expert with 15 years experience, and Nishimura in sales.
Although it is a deformed part, the target shape does not look so complicated. If we make a mold and hit an existing aluminum material, everyone thought it would be easy.
However, I can't do it. It is only a defect that cracks and wrinkles get in as it pop up. Adjuster chain has assembled with cold forged skin as it is with appearance parts, so if cracks and wrinkles are included, the story does not begin in the first place.
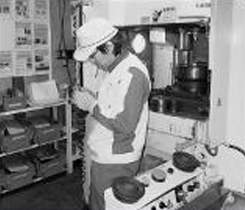
Replace parts made by cutting with cold forging. This brings various benefit to the customer company.
For example, since the material yield has increased and the processing speed has increased by one digit, significant cost reduction could be expected, or more specifically, the strength of part is increased because the material is compressed. The beauty of cold and forged skin also enhances value added of the overall motorcycle appearance.
This a suggestion that even customer company not hope for. For Mr. Nishimura,
as sales representative, it was supposed to be a unique opportunity for Komatsu Kogyo to gain
confidence. However, looking at the completed part (finish good) for the first time, Nishimura got scared.
He could not go to the customer to bring this finish good ....